フランスの高級車メーカーBugatti(ブガッティ)は、高度な製造技術を駆使して、信じられないほど高性能なハイパーカーを世に送り出してきました。そのBugattiが現在活用している技術のひとつが3Dプリントです。同社によると、3Dプリント技術を使って「クモの巣のように細かく正確、なおかつ鋼鉄のように安定している」製品を作ることができるといいます。
Bugattiは「Chiron(シロン)」のPur SportおよびSuper Sport 300+で3Dプリント技術を使用しています。具体的には、チタン製のテールパイプトリムカバーの製造に用いられています。テールパイプトリムカバーは車で最もエキサイティングなパーツというわけではありませんが、3Dプリントされた金属製のカバーは初めて公道での使用が正式に認められました。従来の方法で製造された部品と異なり、高い強度を維持しながら軽量化を実現できるほか、複雑な形状も生成できます。
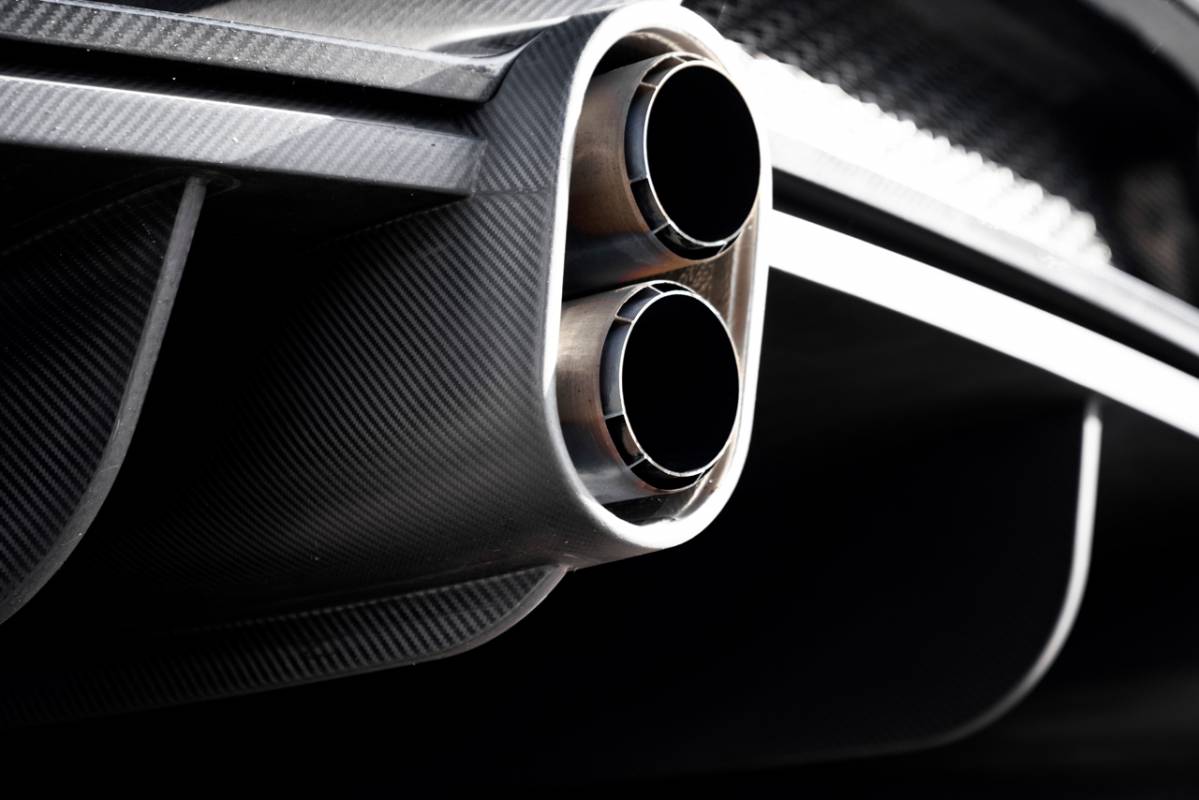
3Dプリントされたトリムカバーの大きさは縦22cm、横48cm、高さ13cmで、グリルとブラケットを含めた重さはわずか1.85kgと、ノーマルのChironに使われているものより1.2kg軽くなっています。製造工程では、チタンを同時にプリントする400ワットレーザーを4つ使用します。
一番薄い部分の厚みは0.4mmしかありません。Bugattiによると、約4200層の金属粉が積み重ねられ、しっかりと融合しているとのこと。多数のフィラグリーストラットで隙間を埋める格子構造により、最小限の材料で製造が可能となっています。
また、開発チーム可能な限りの軽量化とともに部品強度を高めるため、単層部にバイオニックハニカム構造を採用しています。この構造により大きなコンポーネントでも高い表面剛性が得られます。また、カバーは650°C以上の温度に耐えることができるとのこと。Bugattiは2018年から3Dプリントを利用し、ブレーキキャリパーの試作などを行ってきました。
コメントを残す